The first article in this series explained the relevance of low-migration printing, while the second illustrated the effects of this type of printing in practice. The third and final part of the series addresses a number of specific challenges relating to the use of low-migration inks. The focus is not on scientific aspects but on the consequences for day-to-day label printing.
What are low-migration UV inks?
The first thing to point out is that there is no such thing as a migration-free ink. And even if only low-migration inks are used, there is no guarantee that the relevant regulations can be complied with. What's more, low migration is neither an international standard nor a protected term. It is simply a generic term for ink series with optimised migration properties. Compared to physically drying inks (e.g. solvent-based inks), the drying process of chemically drying UV inks is always more problematic and susceptible to errors. Chemically drying inks also have migration weak points, such as the residual oil problem encountered with oxidatively drying offset inks.
Describing the detailed chemical structure of low-migration inks would go beyond the scope of an article focusing on the practical application of such inks. There are, however, interactions in the ink structure that have far-reaching consequences for day-to-day use in a printing press:
- Ink costs: In principle, purer and better coordinated raw materials need to be used for low-migration inks. Both these requirements send raw material costs spiralling.
- Migration properties: The raw materials currently used to optimise migration properties normally slow down the drying process. If the machine speed remains the same, a higher UV drying power is therefore needed than for conventional inks.
- Ink adhesion: Virtually all efforts to optimise an ink's migration properties have a direct negative impact on its adhesive strength (ink adhesion).
The ink manufacturer's aim is thus to find an application-dependent compromise between costs, adhesion and migration. For label printers, this means matching the ink selection even more specifically to the relevant application than before. This is the only way of achieving a reasonable balance between costs and proper functioning in everyday use.
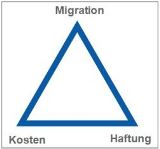
Figure 1: Interactions during the manufacture of low-migration inks
Using low-migration inks in a press
Before converting an existing press to low-migration printing (see article 2), it is advisable to test the ink series in question in the various applications without any production stress. Normally, the printing process no longer reacts in the same way as with conventional inks. The following changes frequently occur in practice:
Reduced ink adhesion: Ink adhesion is often confused with inadequate drying, which is not necessarily always the case. It is advisable to use appropriate test methods to reliably establish the actual cause. If ink adhesion definitely does not meet expectations, the first thing to do is to check the ink's suitability for the relevant application. If no improvement is achieved by using appropriate ink series and/or alternative substrates, the only solution in many cases is to apply primer layers beforehand.
Inadequate surface drying: If the problem is actually inadequate surface drying, the first thing to do is to establish whether the UV power can be increased further still or whether an improvement can be achieved by reducing the speed of the press. If an improvement is observed, the UV installation needs to be checked for correct operation. Problems such as “blind” reflectors, UV tubes with an excessive burning life and any soiling of the quartz glass often only become apparent with low-migration printing.
Inadequate drying penetration: If the boundary ink layer between substrate and ink film does not dry properly, this indicates that too much ink has been applied. Ink manufacturers normally specify the maximum permissible coverage. It is quickly apparent whether reducing the amount of ink applied improves the situation. Here, too, the UV installation needs to be checked for correct operation. It can also help to use doped UV tubes with a more penetrating effect.
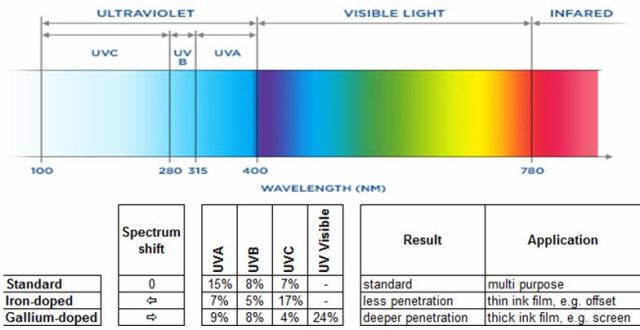
Figure 2: Effect of standard doping (typical overall distribution 30% UV light, 15% visible light, 55% infrared light)
It is advisable to convert an existing press to low-migration printing only once the behaviour of the applications to be produced is known and satisfactory solutions have been found to any problems. If the results are still unsatisfactory, it may be necessary to re-evaluate the drying system. Existing UV drying installations can often be extended to create more powerful installations or completely replaced. When re-evaluating presses, a UV drying installation with nitrogen inertisation can sometimes also be an option. Replacing the oxygen atmosphere in the printing nip with a nitrogen atmosphere (inertisation) significantly improves drying efficiency. It is always worth obtaining advice from the press manufacturer, because it is generally not advisable to mix additives with low-migration inks.
Summary
Low-migration UV label printing is in its infancy. As more experience is gained in dealing with the relevant regulations and implementing them on a day-to-day basis, reliability and efficiency will also improve. In all likelihood, low-migration UV inks will also benefit from further developments and be easier to process in the future.
Migration regulations for packaging are at present restricted to food products, but we can assume that personal hygiene and cosmetics products will also be subject to stricter requirements in the future. It is therefore definitely worth exploring the possibilities offered by low-migration UV label printing.
Large manufacturers of branded goods and retail chains are already ensuring strict compliance with the existing regulations and will continue to do so in the future – in all probability to an even greater extent. Image problems and the costs resulting from contaminated food are an absolute worst-case scenario in the global trend towards “clean foods”. The primary concern of manufacturers of branded goods and retail chains is thus to minimise the risk. Despite all the challenges, low-migration printing also offers label printers the opportunity to stand out on the market over the long term.
Here at Gallus, we are convinced that our products and consulting services can give labels printers a vital competitive advantage in low-migration printing. Gallus is happy to support its customers by recommending materials and providing training, service activities and printing assistance. Please feel free to get in touch. We will be only too pleased to help.